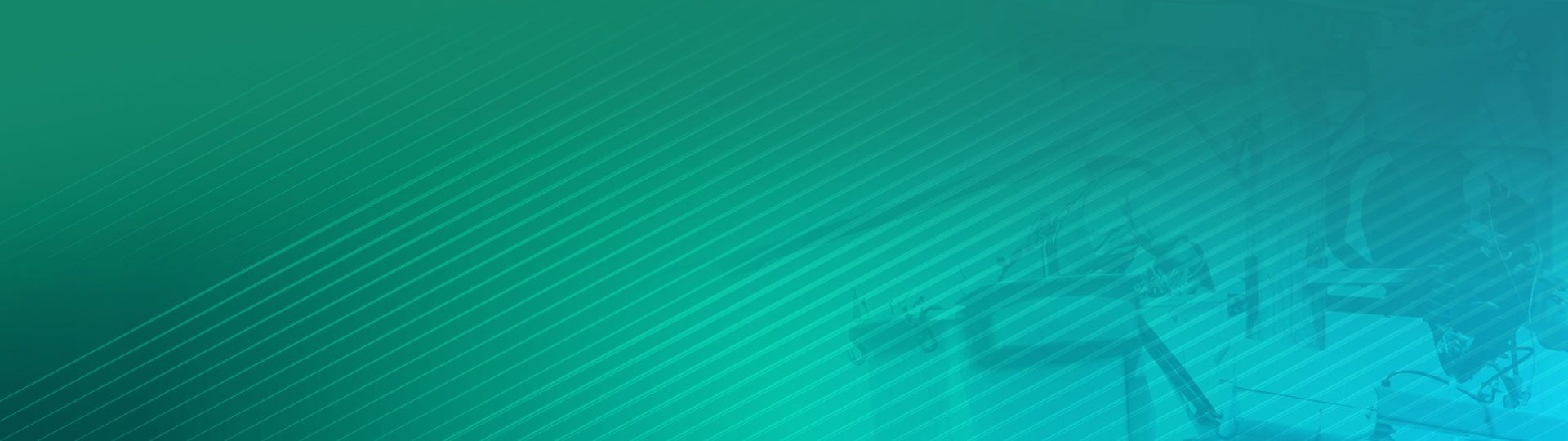
Proving Safety First Works
By Lee Marchessault, CUSP. Incident Prevention Magazine July 2018.
Electrical utilities are among the most hazardous industries to work. This was recognized in the early days of electrical power distribution with extremely high fatality rates. Since those days utilities have examined every injury and fatality to learn how to prevent the next one including analyzing possible hazards, mitigating the hazards identified to a safe level of acceptable risk, created policies and procedures, developed and provided protective equipment, and made the work place as safe as it can be… or have they? Unless we make a conscious effort to verify that what has been developed and provided is used properly, safe work practices can only be assumed. By auditing personnel, or to use a better term conducting field personnel worksite observations, on a consistent basis we can verify and measure the effectiveness of the organizational safety efforts proving that the “Safety First” culture is accurately represented.
Conducting field observations enables the organization to take a firsthand look, and document employees as they demonstrate their knowledge and ability to work safely, and also sends a message to the employee that the company cares about their safety. To effectively conduct a worksite observation, plan on being there for no less than 1 hour, and if more than one crew is present, 2-3 hours may be best.
Why Perform Worksite Observations
When a new employee starts they will likely go through some level of orientation to understand the company benefits, learn expectations. They are usually given a safety manual and company-provided tools required to get started. Once the apprenticeship or trainee period is completed, the only formal training he/she may get is some type of regular safety training. OSHA states in the training section of the utility standards 29 CFR 1910.269(a)(2)(iii):
“The employer shall determine, through regular supervision and through inspections conducted on at least an annual basis, that each employee is complying with the safety-related work practices required by this section.”
This is in itself will justify and even mandate the need to conduct worksite observations. All field personnel who work with electrical equipment should be part of the program including meter personnel, power plant operators, line workers, substation electricians and relay technicians.
Other benefits of performing observations include identifying:
- Training deficiencies
- Policy or procedure deficiencies.
- Provide training in the moment if necessary and discuss hazards and associated risks
- Equipment deficiencies also including pre-work inspection process and use
- Safe work practices (good time to recognize the employee or team and also provides key information to improve safety practices universally)
- If the safety culture is where is should be
Preparing for the Observation Program
Before starting an observation program, it’s important that there is buy-in from the top. Take the CEO and other senior management personnel on a few field observations regularly. Be sure they understand the PPE requirements as they enter the workzone such as steel toe boots, workzone vests, hardhat and safety glasses. This will support acceptance by field personnel to the program and help change or strengthen the safety culture of the organization.
Another important consideration before you begin is to look at the corrective action policy. If you have a policy that states a letter of reprimand is written for any safety infraction, it will be tough to get the program off the ground. You may need to negotiate a new or addendum policy to allow for coaching for minor infractions. Major life threatening infractions will need to be addressed more firmly. The key to corrective action is that it should be consistent. On the flip side, it is important to provide plenty of positive feedback for good safe work practices. Once the observation is done, share the score with all field personnel and emphasize the good work practices. This will foster future safe work practices also improving the safety culture.
The form and format has to be well developed with a scoring system that is as objective as possible to prevent inconsistencies among the various supervisors conducting the observations. It should be a simple checklist that won’t take much time to look away from the work. Electronic versions that are downloadable to smart phones work ok but are sometimes tough to see in the sunlight and take more time away from the observation part. The outcome should be measurable and quantifiable. Separate the observations into parts such as tools and equipment, personal protective, and work practices. By measuring these items separately it will help to target deficiencies directly and develop a means to correct efficiently and effectively. The scoring system should be weighted according to the level of risk (i.e. 1- minor, 3 – moderate, 10 – major). Of course if a high risk hazard is identified with unsafe work practices, immediate shut down on the job should be done. The scores for infractions are then deducted from 100. This is a system that is understandable by everyone and does not need to be weighed. Typically a score of 90-100 is very good, 80-90 is good, 70-80 will need some work, 60-70 indicates a condition that should be addressed ASAP, and under 60 would require an immediate safety shutdown. The following example of a work practice deficiency was observed in a real life incident. An Apprentice Line Worker was seen with a digger bar trying to free up a pole butt where an old pole was removed to about 4 ft. off the ground. A digger/derrick operator was unsuccessfully attempting to pull the pole butt using the winch line with a choker connection on the pole while the apprentice was digging. This prompted an immediate shut down. If the pole was suddenly released, the tension could have caused the pole butt weight of perhaps 200 pounds to fly up and spring back striking the apprentice, or if the winch line failed, the line could have seriously injured him. The corrective action following the shutdown was to purchase the proper tools to pull the butt and train employees.
Who Performs the Observations
Worksite observation programs are best done by Operations Supervisors and occasionally their Managers with spot checks from the Safety Managers or neutral qualified designees who don’t work directly with the managers or those being observed. Safety management should facilitate the program but should not conduct all personnel observations. Supervisors performing observations in the field provide time to connect with field personnel and give them an opportunity to praise them for the safe work practices identified.
In order to be consistent, those assigned to perform field observation should be trained on how to conduct the observation including:
- What actions, equipment, PPE, work practices to look for
- Implementing corrective action and coaching when infractions are identified.
- Methods of rewarding safe work practices
- How to deal with different types of personalities
- Scoring the observation while in the field (understanding the probability/severity matrix)
Taking digital photos throughout the process may be beneficial. These can be used at a later time for training. It is important to note that photos used against an employee for violations would be extremely detrimental to the program, so try to use caution on the type of pictures and when or where you use them.
If infractions or deficiencies related to behavior, take corrective action immediately and verbally in a one-on-one format but never in front of other employees.
Tracking and Trending
After the observation is done it should be input into a tracking system that will provide reporting capabilities. This may be developed by the safety department or they may purchase a commercial program. This should have the capability to measure leading indicators or identify unsafe trends to help target at risk areas. The results (leading indicators) may also be used as an incentive program to promote safe work practices. Be careful not to tie incentives to OSHA rates (lagging indicators) as OSHA frowns upon this practice. Reports generated can provide valuable information to show upper management or regulatory agencies the effective of the company safety program.
Summary
Field observations are required by OSHA, but more importantly provide a valuable tool for companies to determine if the training provided is effective, tools and equipment are adequate, and the safety culture is where it should be. If done properly, this process is more powerful than any classroom training and provides a solid foundation to an exemplary safety culture.
Lee Marchessault is the President of Workplace Safety Solutions, Inc. For questions, he may be contacted at lee@workplacesafetysolutions.com